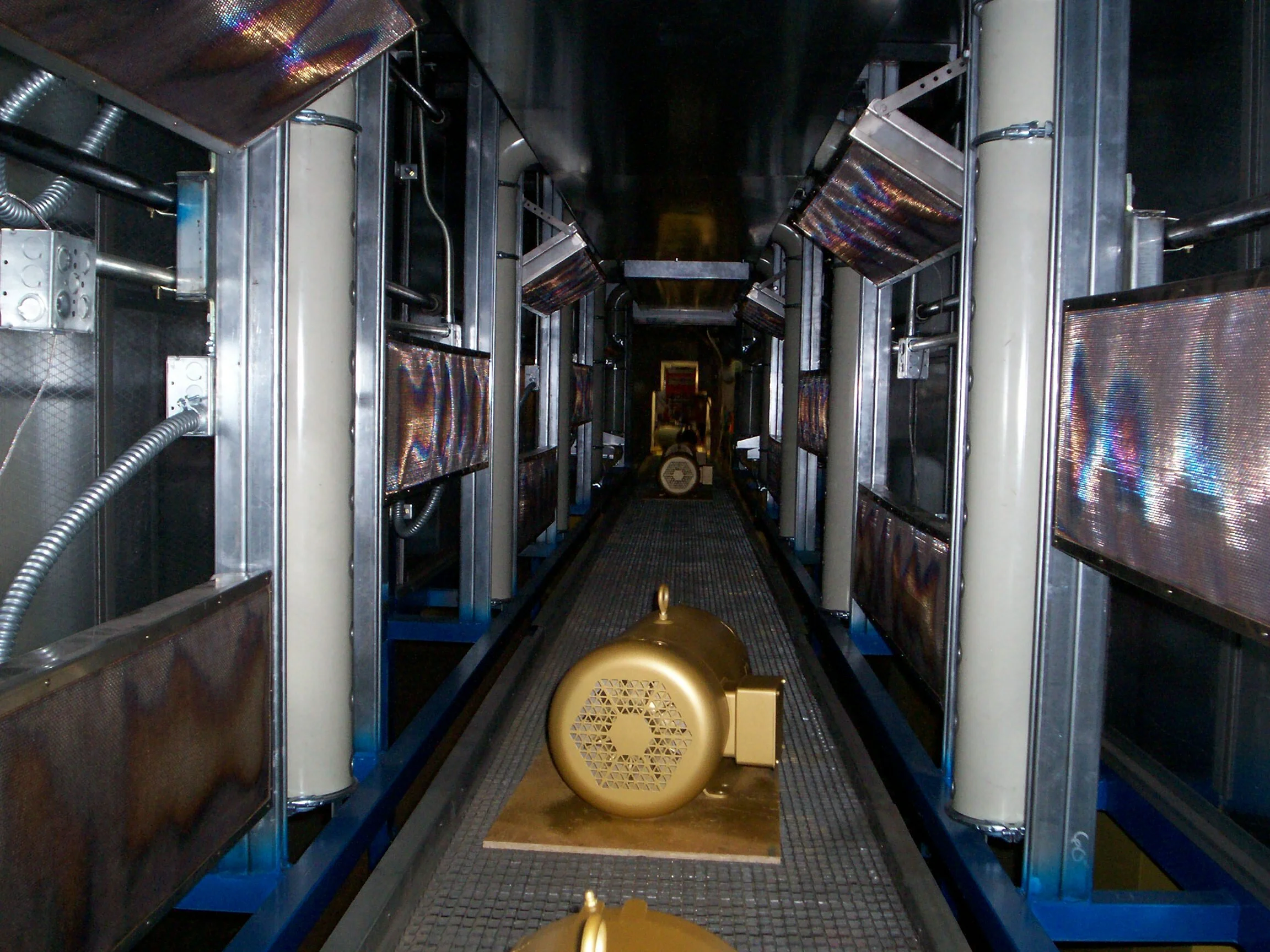
liquid coating
increase production, Save space & reduce operating costs
Catalytic Industrial Systems gas catalytic infrared heating solutions are perfectly suited to liquid based coating applications. Liquid based coating absorbs the infrared energy more readily without the need to heat up the entire substrate material. This reduces the time and energy required to uniformly cure the coating.
liquid coatings
Catalytic industrial infrared ovens have long been a leading choice for the uniform, efficient cure of solvent and waterborne coatings and adhesives. Gas infrared cures both solvent and water based coatings up to 10 times faster than conventional drying. Our customers see increased production, reduced oven footprint and savings on utility costs.
Catalytic industrial infrared ovens distribute heat evenly, and are well-suited to parts with complex shapes. Heat energy is moderate, rather than high intensity, so convection is compatible with many substrates.
solvent based paints
Solvents contain higher levels of organic compounds compared to water-based coatings. When these compounds evaporate, they release Volatile Organic Compounds (VOC’s) into the atmosphere resulting in a strong odor and toxic impact on the environment.
Solvent-based paints typically requires some sort of flash. Solvents need to be released before entering the final cure oven, to prevent solvent pop or bubbles from forming. Catalytic Industrial infrared ovens can reduce or eliminate these common conditions by curing from the inside out.
Water Based Paints
Advances in paint technology mean that water-based paints are in many ways equal, or superior to their solvent-based counterparts. Water-based coatings have moved into the industrial applications, including maintenance coatings for steel and concrete.
Water readily absorbs infrared radiant energy at 3, 4.5 and 6 microns wavelength. Thus, gas catalytic IR is a perfect fit for curing water-based coatings. CIS heaters generate “far infrared” with the wavelength of 3 to 7 microns. When curing water based coatings the catalytic infrared will target the water in the paint and evaporate it much faster than conventional ovens.
Process improvements & Savings
cis helps TEXAS Engine Maker reduce curing from 60 to 20 minutes
Our customer, an international heavy industrial equipment Fortune 100 corporation located in South Texas manufactures and paints large diesel engines for large mining vehicles. They reached out to CIS with an oven and curing challenge to reduce curing time. The previous process used a 150 feet long convection oven with two 1.5 million BTUH burners that required 50-60 minutes curing time.
After testing in the CIS lab with multiple models of engines, a time and energy saving solution was developed. CIS demonstrated that the cure could be achieved in only 20 minutes with Gas Catalytic IR using only half the energy. CIS’ gas catalytic system was retrofitted into the existing convection oven. The new system improved the process using only 50 feet of space in 1/3 the cure time while consuming half the energy.
Projects
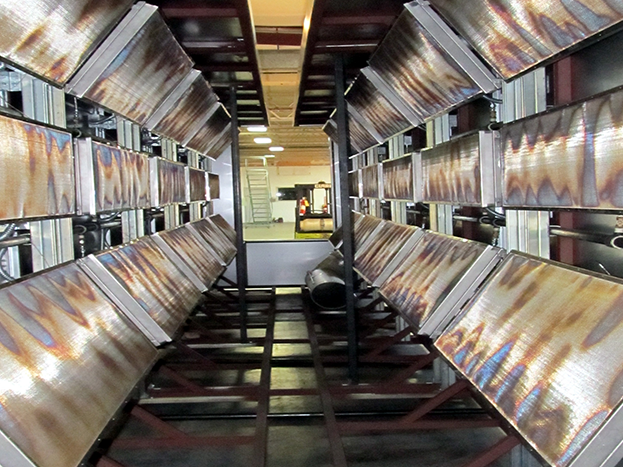
Ship Builder | Solvent Coating
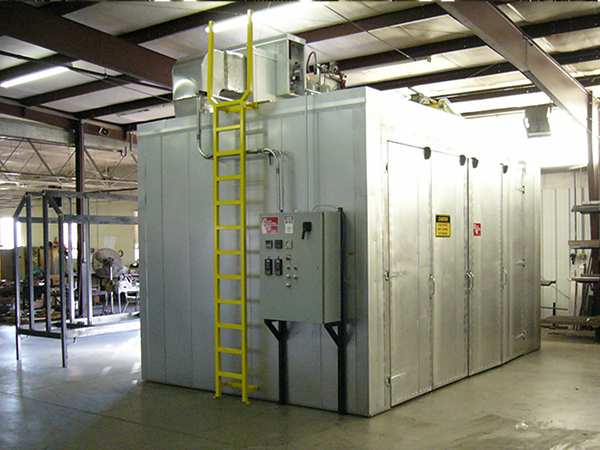
Wire Manufacturer | Convection

Agriculture Equipment | Paint Curing

Motors | Solvent Based Coating
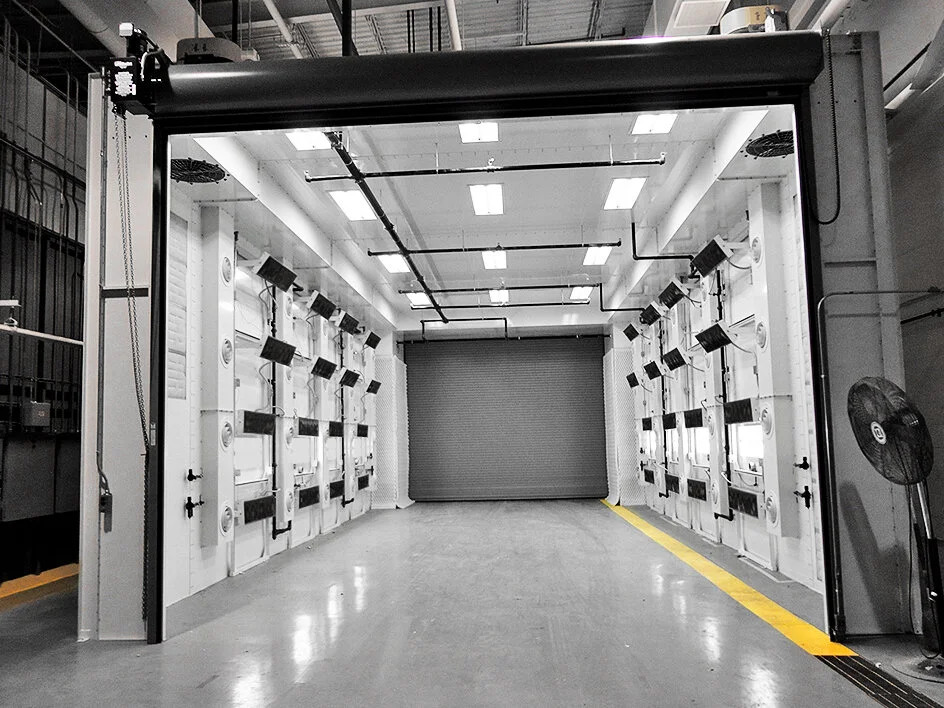
Vehicles | Curing Water Based Paint
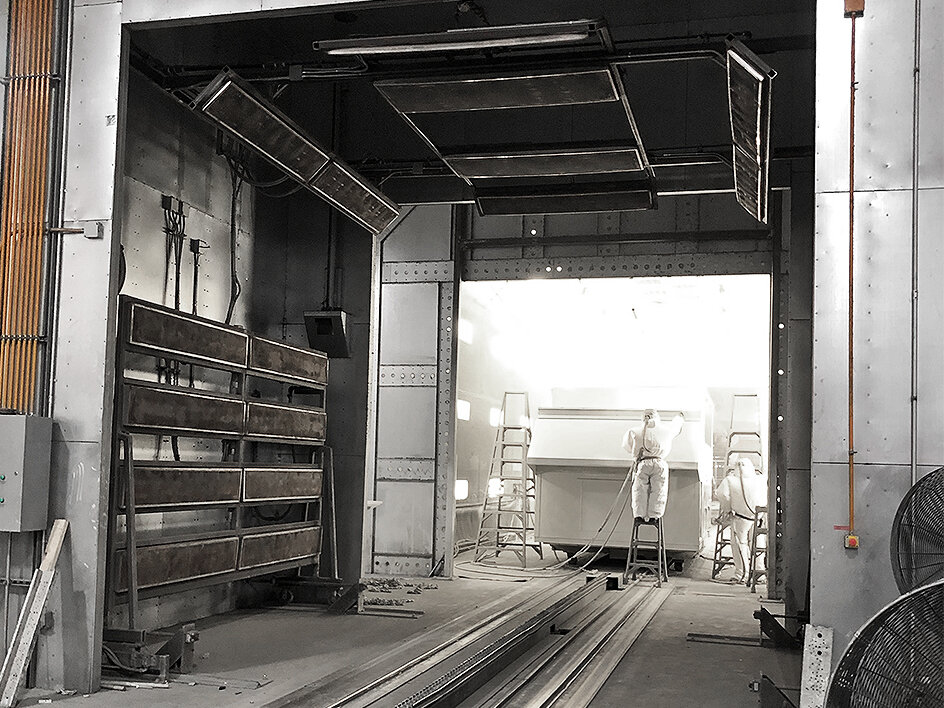
HVAC | Paint Curing Oven
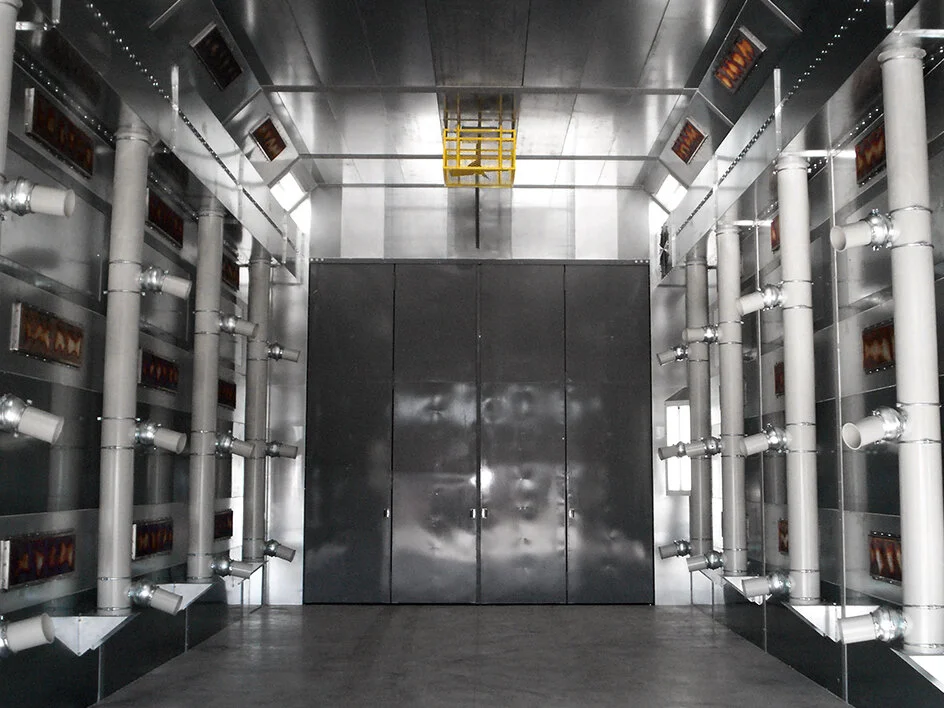
Military Vehicle | Paint Curing

Wind Turbine | Paint Curing